The proposed system includes a hardware-based solution (type A) and the option for HRS operators to send a signal from their refueling stations to update a web-based platform (type B).
Type A stations use the HRS availability transmitter (HRS-AT) to collect the availability and maintenance signals from the plant control system via 24 V digital inputs (DIO module). In order to prevent malicious operations, there is no interaction with the control system. The HRS availability transmitter is based on an industrial grade micro-computer (Revolution Raspberry Pi) with standardised connectors for up to 10 input signals and is designed for use in typical switchgear construction, with DIN rail mounting and 24 V DC power supply. If 24 V DC power supply is unavailable on site, an external power supply unit can be mounted alongside the transmitter. Similarly, an external cell modem may be mounted wherever no local internet connection is available. The signals are transmitted via an encrypted channel to the cloud based EU HRS platform.
Type B stations do not require additional hardware to transmit a signal from the site to the HRS availability platform. The existing vendor-specific monitoring systems are already connected to on-site control systems and are used to send a periodic availability signal to the EU HRS availability platform. The signals of both the german legacy system (Cumulocity) and NEL are fetched by their preexisting pull interfaces, while ITM uses the standardised EU-Push-API. The metrics are gathered directly on the monitoring server via Icinga 2 check commands.
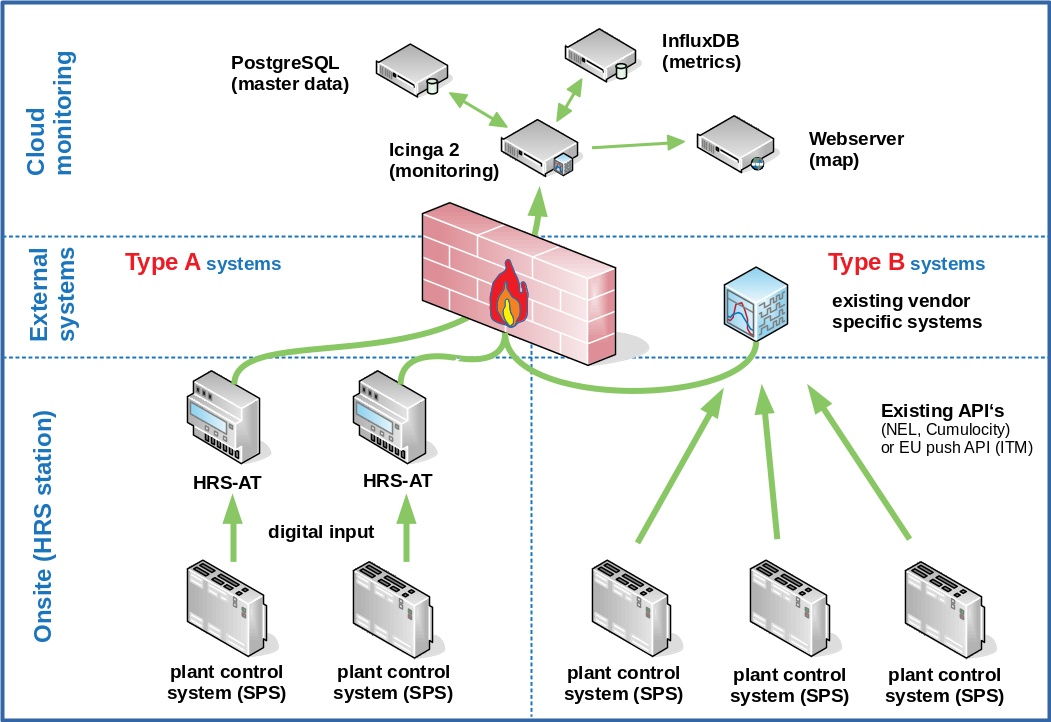